The mirror grinding on the surface grinding
machine often produces defects such as surface ripples, burns, scratches,
patterns, and wear marks (wire flow). For these problems, the following
measures can be taken:
1. The surface ripple is mostly caused by
the vibration of the grinding wheel, such as excessive bearing clearance,
eccentricity of the main shaft, poor dynamic balance of the motor rotor, uneven
oil film between the main shaft and the bearing. In addition, poor balance of
the wheel can also produce ripples. If the wheel is well balanced and there are
still ripples, it is necessary to overhaul or adjust the wheel and its
associated parts to completely eliminate the ripple phenomenon.
2. When the material with high hardness is
processed, the grinding efficiency of the grinding wheel is poor, the grinding
point will generate high temperature, and the workpiece will be easily burned
(for example, when grinding the W18Cr4V, burns are more likely to occur). In
order to prevent burns, there must be sufficient grinding fluid at the grinding
point. In addition, the amount of back eating knife should also be appropriate,
should not be too large. The best way is to reduce the line speed of the
grinding wheel, about 18m/s or so. Using the low speed of 1440r/min on the
M7120A grinder basically eliminates burns. Another advantage of reduced wheel
speed is that it reduces wheel frame vibrations, which in turn reduces and
eliminates ripple.
3. There are two kinds of scratches in
mirror grinding: There is no regularity of scratches. This is because the grinding
liquid is impure, and impurities and abrasive grains that are brought out are
scratched between the grinding wheel and the workpiece. The method to eliminate
such scratches requires the grinding fluid to be filtered. Generally, magnetic
and copper meshes are used for three-way filtration. The other scratches are
lined like a dotted line, and are shallow. The distances are approximately the
same. This is a grinding wheel. When the grain is about to fall off, it gets
scratched as the grinding wheel rotates. The elimination method at this time is
to use a sufficient grinding fluid when dressing the grinding wheel, and to
make the two ends of the grinding wheel into an oblique shape with a narrow
outer width. In addition, the choice of grinding wheel should also be
appropriate, not too soft, do not use too good grinding wheel. .
4, when the mirror grinding, easy to appear
in many shapes. There are many factors that cause patterns. The main cause is
vibration. Among them, there are periodic vibrations of the grinding wheel,
external influences and vibrations of neighboring machine tools. When the wheel
is blunt, the pattern may also appear when the stroke is unstable. Grinding is
performed when the adjacent machine tool is not started, and the pattern is less
likely to appear.
5. When the wear marks (wire flow) in
mirror grinding are obvious, to remove this kind of wire flow, you have to use
fine-grained grinding wheels. However, when using fine-grained wheels, the
following points must be taken into account:
① When sharpening the grinding wheel,
the diamond knife must be sharp and the grinding fluid should be sufficient to
wash away the debris in time so as not to affect the surface of the grinding
wheel.
② The amount of grinding should be
appropriate to prevent surface burns and other ills from affecting the
smoothness of the surface. Pay attention to the appropriate grinding allowance.
③ The wheel speed must be reduced to 15
to 18 m/s.
④ Grinding fluid is tightly filtered to
prevent scratches.
⑤ When finishing the grinding wheel with
a grinding stone, the contact area between the grinding stone and the grinding
wheel should not be too small, and the grinding stone used should not be too
soft, otherwise it will not function as a finishing wheel.
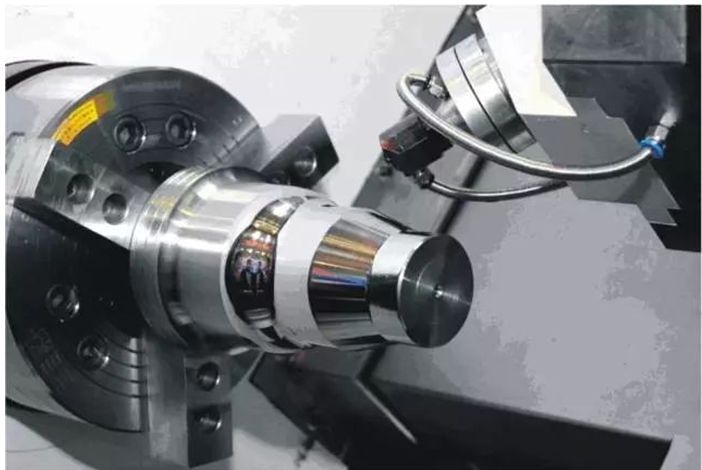